插铣法常见的使用场景
1、当刀具悬伸大于4xDc
2、当稳定性差时(如由于振动不能进行侧铣)
3、圆角半精加工
4、加工钛合金等难切削的材料
5、当机床功率或扭矩有限时
插铣可以向下进给,也可以向上进给,如用三面刃铣刀向上进给加工下平面。由于刀杆刚性高,刀具的悬伸长度大,插铣深度可达到铣刀直径的4~6倍,而且不会产生振动,因此非常适合插铣深腔、立直面、窄槽、深槽及形状复杂的型面。
注意:在有利情况下,由于金属去除率较低,插铣不作为首选。
插铣法
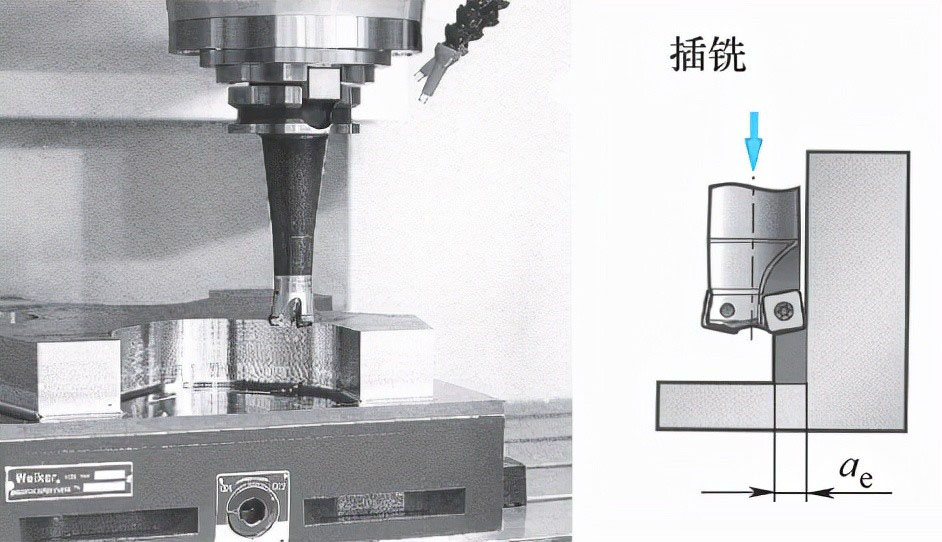
Z轴铣削法
插铣法又称为Z轴铣削法。通常铣削时使用最多的是纵向(X轴)进给进行铣削,其次是利用横向(Y轴)进给进行铣削。插铣是利用铣刀的底刃作为主切削刃,工作台上升即进给方向沿着铣刀轴线方向(Z轴)进行切削加工,将工件中的余量切除。
插铣法特点
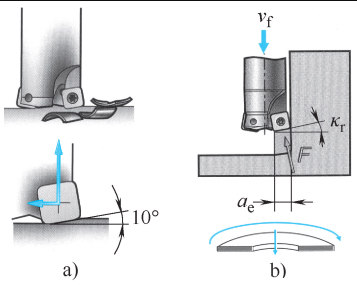
插铣切削力与切屑
1)增加刀杆刚性
插铣是利用铣刀的端面切削刃作为主切削刃进行切削,主偏角κr=10°(上图a),因此铣刀承受进给力占90%以上,使得刀杆刚性增加。
2)提高刀具使用寿命
传统铣削是用侧刃切削,产生的切屑由薄到厚或由厚到薄,切削刃在一次切削过程中,切削力变化很大,因此受到较大的冲击,这对高硬度、脆性大的刀具是十分不利的。而插铣是用端面切削刃进行切削,刀具高速旋转,轴向进给很慢,刀齿切入和切出时,产生的切屑厚度基本是等厚(上图b),切削刃受到的切削力是均衡的,这样可减少刀具产生崩刃破损,提高刀具使用寿命。
3)节省换刀具时间
插铣时铣刀可钻可插,一刀两用。在铣削凹型面时,可用插铣刀先钻孔,然后插铣平面和各种型面,节省换刀具时间。
4)工件变形小,切削平稳
插铣是轴向进给,背向力小,即使采用大吃刀量插铣立面,让刀量也很小,工件变形小,切削平稳。
5)适合圆角半精加工
用立铣刀铣圆角,由于在转角处切削面积突然增大,背向力大,产生“扎刀”。用插铣刀来插圆角,由于主切削力是进给力,背向力减小到10%左右,插铣可以顺利完成。
6)背向力小
插铣时背向力很小,消耗铣床功率小,可以弥补铣床功率不足,减轻主轴轴承磨损。
7)可实现高效加工
插铣可以实现高速、强力铣削,每齿进给量可以达到0.15~0.25mm/z,可以快速切除较大的切削余量,比径向铣削效率提高4~5倍。总体来说,无论是小批量的生产,还是大批量的零件制造,插铣法都是一种高效率的铣削方法。
插铣刀1)增加刀杆刚性
插铣是利用铣刀的端面切削刃作为主切削刃进行切削,主偏角κr=10°(上图a),因此铣刀承受进给力占90%以上,使得刀杆刚性增加。
2)提高刀具使用寿命
传统铣削是用侧刃切削,产生的切屑由薄到厚或由厚到薄,切削刃在一次切削过程中,切削力变化很大,因此受到较大的冲击,这对高硬度、脆性大的刀具是十分不利的。而插铣是用端面切削刃进行切削,刀具高速旋转,轴向进给很慢,刀齿切入和切出时,产生的切屑厚度基本是等厚(上图b),切削刃受到的切削力是均衡的,这样可减少刀具产生崩刃破损,提高刀具使用寿命。
3)节省换刀具时间
插铣时铣刀可钻可插,一刀两用。在铣削凹型面时,可用插铣刀先钻孔,然后插铣平面和各种型面,节省换刀具时间。
4)工件变形小,切削平稳
插铣是轴向进给,背向力小,即使采用大吃刀量插铣立面,让刀量也很小,工件变形小,切削平稳。
5)适合圆角半精加工
用立铣刀铣圆角,由于在转角处切削面积突然增大,背向力大,产生“扎刀”。用插铣刀来插圆角,由于主切削力是进给力,背向力减小到10%左右,插铣可以顺利完成。
6)背向力小
插铣时背向力很小,消耗铣床功率小,可以弥补铣床功率不足,减轻主轴轴承磨损。
7)可实现高效加工
插铣可以实现高速、强力铣削,每齿进给量可以达到0.15~0.25mm/z,可以快速切除较大的切削余量,比径向铣削效率提高4~5倍。总体来说,无论是小批量的生产,还是大批量的零件制造,插铣法都是一种高效率的铣削方法。
插铣刀
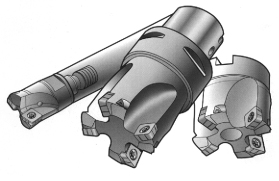
插铣刀
插铣刀是利用底刃进行切削,底刃是主切削刃,切屑是从底刃前方排出,因此插铣刀应采用少齿,以便留有较大的容屑和排屑空间。
插铣刀
插铣刀使用方刀片时,主切削刃倾斜角度为0°~10°,方刀片(iC9mm、14mm)适合高速插铣淬硬钢、高强度钢。使用圆刀片,切削刃强度高,抗冲击,刀具寿命高。圆刀片(直径(iC8mm、10mm、12mm、16mm)适合插铣钛合金和高温合金。
铣刀直径与刀片数量关系表
切削用量的选择
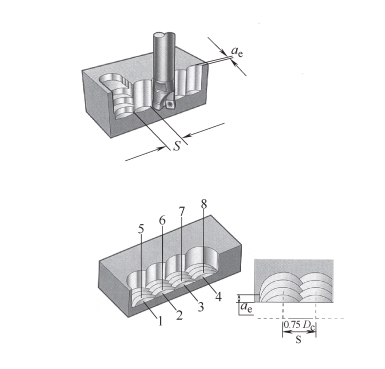
插铣切削用量
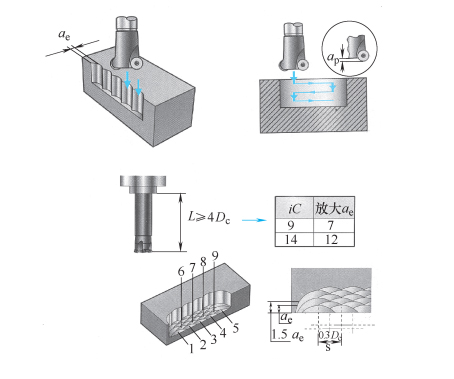
插铣切削用量
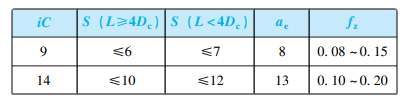
方刀片插铣切削用量(单位:mm)
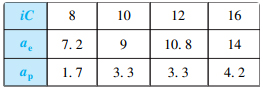
圆刀片插铣切削用量(单位:mm)
最后,如果是专门做铝板加工,更建议大家使用专门的
铝加工中心(Hassfull
F90精密加工中心哈思孚)。加工速度更快,在保证加工精度范围的基础上对通用加工中心做了配置优化,更适配工业领域的铜铝这类软金属以及PC、PA、POM、PEEK、电木板、FR4、千思板、抗倍特板之类非金属的CNC加工,购买价格和维护成本上会比通用加工中心低得多,很适合大批量快速加工。